Innovación en la producción de materiales compuestos:
el uso del grafeno en la pultrusión
Los compuestos poliméricos reforzados con fibra son utilizados ampliamente en los sectores aeroespacial, automovilístico, naval y de generación de energía eólica debido a sus propiedades de ligereza y alta resistencia mecánica. Estos materiales son una alternativa en auge para sustituir a otros materiales como los metales.
En la actualidad existen diferentes métodos para la fabricación de compuestos reforzados con fibras, entre los que destaca el método de pultrusión. Un método altamente eficiente y automatizado que permite el control de los parámetros del proceso (mayor precisión y exactitud), reduciendo la variabilidad en la producción de las piezas.
La pultrusión es un proceso de producción de materiales reforzados donde se pueden distinguir dos componentes, la matriz o fase continua y el refuerzo o fase discontinua. La matriz actúa como un agente de adhesión, en la que el refuerzo queda embebido. Las funciones de la matriz, es transferir la carga a las fibras, mantener las fibras en su posición, evitar la propagación de fisuras, proveer propiedades físicas y químicas del compuesto y también delimita el rango de temperatura que podra soportar el material compuesto. La matriz es termoestable o termofija (poliéster insaturado, resinas epoxi o resinas vinil-ester). Por otro lado, el refuerzo tiene como propósito agregar alguna propiedad que la matriz no posea, como incrementar la resistencia mecánica, la rigidez, la resistencia a la abrasión o mejorar su desempeño cuando es expuesto a temperaturas elevadas. La eficiencia del refuerzo es mayor, cuanto menor sea el tamaño de las partículas o el diámetro de la fibra y más homogéneamente estén distribuidas en la matriz. Las fibras más utilizadas son de vidrio, carbono y aramida debido a su alta resistencia de tracción.
El proceso de pultrusión (Figura 1), es continuo y se utiliza para la fabricación de piezas con un perfil transversal constante, como postes, varillas, molduras automotrices, etc. En la primera etapa de alimentación las fibras de refuerzo pasan por una placa perforada para su alineación, después pasan por un pre-moldeo donde se agrega un tejido para reforzar la fibra. Después en la segunda etapa, las fibras se impregnan de resina liquida y pasan a una etapa de pre-formado donde se orientan las fibras antes de entra al molde. En la tercera etapa (moldeado), se da forma a la sección transversal de la pieza y mediante la aplicación de calor se endurece la resina. Durante la aplicación de calor en el molde, hay tres fases: pre-calentamiento de la matriz y del refuerzo, activación del catalizador de polimerización y curado del material. Después, el perfil sale del molde como material termofijo y pasa hacia un mecanismo de tracción continuo que tira o jala el material a una velocidad constante (cuarta etapa)). Finalmente, en la quinta etapa, una sierra de disco corta el perfil con la longitud deseada. El perfil del compuesto reforzado obtenido es un material completamente rígido, que no se reblandece e insoluble con capacidad de soportar temperaturas elevadas.
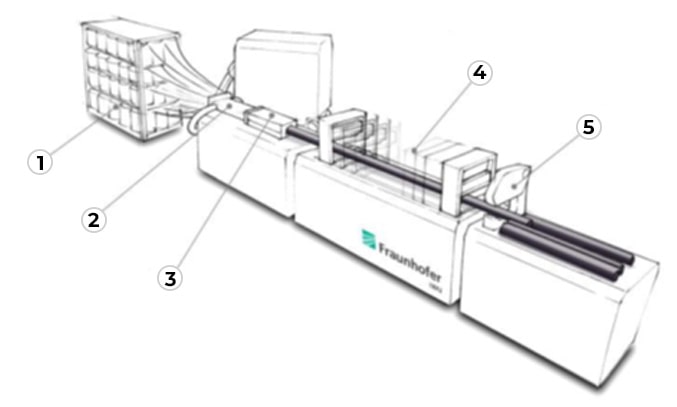
Actualmente las principales aplicaciones de este proceso se centran en la fabricación de materiales para la construcción, transporte y consumibles, por ejemplo: construcción de vehículos, aislante térmico, conductos para cable, cubiertas y rejillas para plantas de tratamiento de aguas, perfiles para vigar, fachadas de edificios, ventanas, puentes, escaleras, entre otros.
Sin embargo, aún existen limitantes en esta tecnología, la baja interacción química de la fibra con la matriz (resina) conduce a una fuerza de unión de interfaz débil entre ambas fases (baja adhesión química), lo que hace que hace que el comportamiento de cizallamiento interlaminar y desempeño de los materiales compuestos no sea del todo satisfactorio. Es decir, si la matriz es frágil se puede generar una rotura espontánea, este comportamiento permite medir la resistencia a la cizalladura interlaminar. Dependiendo del tipo de rotura, se puede caracterizar la resistencia del material de la matriz o la calidad de la unión fibra-matriz.
En años reciente, se ha reportado que la introducción de óxido de grafeno (GO) funcionalizado sobre la superficie de las fibras es un método eficaz para mejorar las propiedades interfaciales de los materiales compuestos, ya que la gran área superficial del óxido de grafeno permite cubrir la superficie de las fibras, incrementando la fuerza de unión química entre la fibra y la matriz, mejorando con ello la resistencia mecánica de los compuestos reforzados. Además, el óxido de grafeno ayuda a mejorar la resistencia a la fractura interlaminar del material compuesto, inhibiendo la iniciación y propagación de grietas.
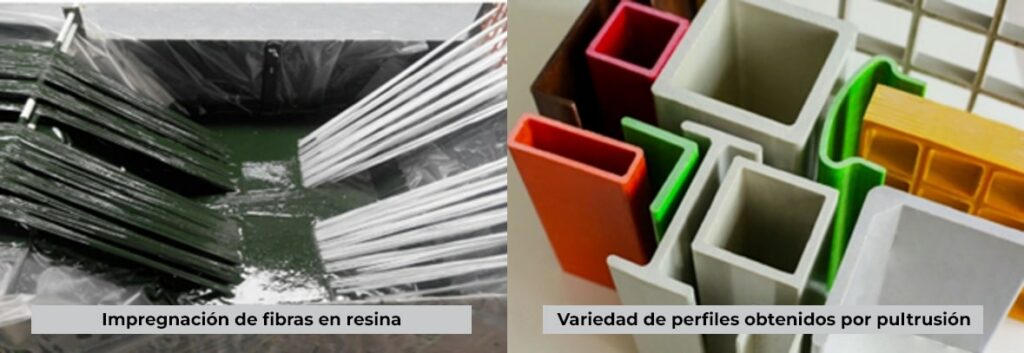
La adición de óxido de grafeno a los compuestos poliméricos reforzados ofrece numerosas ventajas para el desarrollo de materiales avanzados en una gran variedad de aplicaciones debido a su gran área superficie, la cual tiene un fuerte impacto sobre las propiedades de resistencia mecánica, mejorar en gran medida propiedades tales como módulo, tenacidad y fatiga. Por otro lado, el óxido de grafeno puede proveer a los compuestos mayor resistencia al fuego. Su eficiencia está asociada que el óxido de grafeno tiene un fuerte efecto barrera, alta estabilidad térmica y gran capacidad de absorción superficial que son favorables para reducir eficazmente la transferencia de calor y masa.
Actualmente Energeia – Graphenemex®, empresa mexicana lider en América Latina en investigación y producción de materiales grafénicos para el desarrollo de aplicaciones a nivel industrial, tiene a la venta grafeno y óxido de grafeno que puede incorporar o dispersar en cualquier matriz (resina) durante el proceso de pultrusión y con ellos mejorar las propiedades mecánicas de los perfiles o productos.
La incorporación de materiales grafénicos (grafeno, óxido de grafeno) en el proceso de pultrusión, brindan mejoras en las características del producto final, que incluyen:
- Mayor resistencia a la tracción. La resistencia a la tensión puede incrementar hasta en un 30% con respecto a un perfil estándar sin grafeno.
- Producción de perfiles de menor peso, ya que el grafeno permite reducir el peso del producto sin afectar sus propiedades mecánicas.
- Perfiles con mayor módulo de elasticidad.
- Mayor resistencia a la corrosión y propiedades ignifugas.
- Mayor resistencia a fracturas o fisuras.
Referencias
- Yuxin He, Qiuyu Chen. Effect of multiscale reinforcement by fiber surface treatment with polyvinyl alcohol/graphene oxide/oxidized carbon nanotubes on the mechanical properties of reinforced hybrid fiber composites. Composites Science and Technology 204 (2021).108634.
- Jonas H. M. Stiller, Kristina Roder, David Lopitz. Combining Pultrusion with carbonization: Process Analysis and materials properties of CFRP. Ceramics 2023, 6. 330-341.
- Dittrich B, Wartig K-A, Hofmann D, Mu¨lhaupt R, Schartel B. Flame retardancy through carbon nanomaterials: carbon black, multiwall nanotubes, expanded graphite, multi-layer graphene and graphene in polypropylene. Polym Degrad Stab 98:1495.