Graphene oxide:
the new ally of primary coatings in corrosion protection
Corrosion is an electrochemical reaction that occurs when the metal reacts with the surrounding environment forming ferric oxide, causing the metal to lose its main characteristics of hardness and resistance. Oxygen, temperature, humidity, contaminants, gases, and the physicochemical characteristics of water are the main factors that affect the rate at which metals corrode.
One of the most widely used methods to control corrosion is the application of protective (primer) coatings to metal surfaces. The coating forms a barrier between the substrate (metal) and the surrounding medium, retarding the deterioration or oxidation of the metal. The coatings are polymer-based substances (paints), resistant to degradation, which are used to cover the material to be protected.
Nowadays, a wide variety of primers have been developed based on different types of resin, such as the alkyd and epoxy type. Efficiency is generally associated with an increase in cost. Unfortunately, most of these coatings or paints are not perfect barriers and eventually fail due to holes or micropores in the coating or the diffusion of oxygen and water through it (they are not completely waterproof). On the other hand, the coatings continue to have low thermal resistance and above all a limited chemical resistance.
Currently Energeia – Graphenemex®, a leading Mexican company in Latin America in the research and production of graphene materials for the development of industrial applications, through its Graphenergy line, has launched a range of primers and other nanotechnological coatings.
Graphenergy anticorrosive primers are coatings based on graphene oxide (GO), a new nanotechnological additive that provides multiple properties to coatings, including extraordinary corrosion protection and barrier technology (barrier effect). Graphene oxide creates pathways that are very tortuous, which prevents oxygen and water molecules from diffusing through the coating and eventually reaching the metal surface, providing protection against corrosion (Fig. 1). These primaries can act as mentioned, by (1) forming a barrier, which greatly prevents the penetration of oxygen and water molecules, or (2) the inhibition of the corrosion process, by increasing the electrical and ionic resistivity, cutting the corrosion cycle.
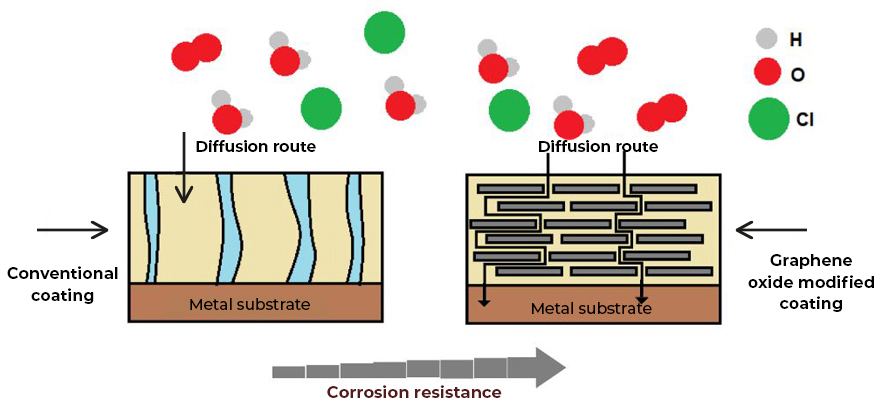
Among the anticorrosive primers that are currently for sale by Graphenergy, there are two: “Graphenergy anticorrosive alkyd primer” and “Graphenergy anticorrosive epoxy primer”, each one designed according to different needs and conditions.
A. Graphenergy anticorrosive alkyd primer.
Provides high anticorrosive protection, resistance to UV rays and provides extraordinary adherence to the substrate. Ideal for the protection of industrial infrastructure, for the application of ferrous surfaces, both for interiors and exteriors. It is recommended for non-coastal areas or where humidity conditions are not high.
B. Graphenergy anticorrosive epoxy primer.
In addition, this coating offers extraordinary chemical resistance, with high wear resistance, resistance to UV rays, impermeability and greater adhesion, in order to improve the useful life of any metal surface or installation and reduce maintenance costs.
Graphene coatings provide enhanced properties and many more benefits, including:
- Higher performance than existing coating technologies on the market today.
- Fewer applied coating layers are required and with higher anti-corrosion protection.
- Zinc reduction in formulations can reduce the amount by up to 50%.
- Primers with greater chemical resistance and high thermal resistance.
- Coatings with greater impermeability and non-stick effect (dirt does not adhere to it). Graphene oxide creates a two-dimensional network on the surface of the coating, which does not allow the anchoring or diffusion of water molecules or chemical substances, which allows the development of coatings with a hydrophobic effect, resulting in coatings that are easier to clean (See Fig.2).
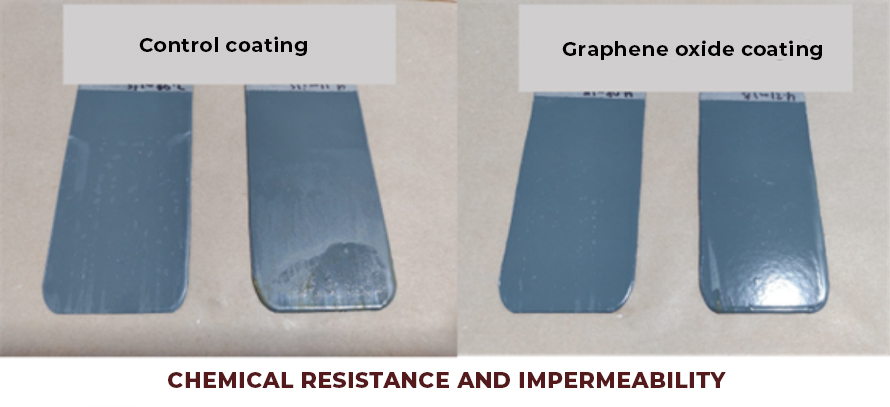
- Improves adhesion to the substrate. The primers with graphene oxide increase their adherence by up to 50% with respect to the control (Fig. 3).
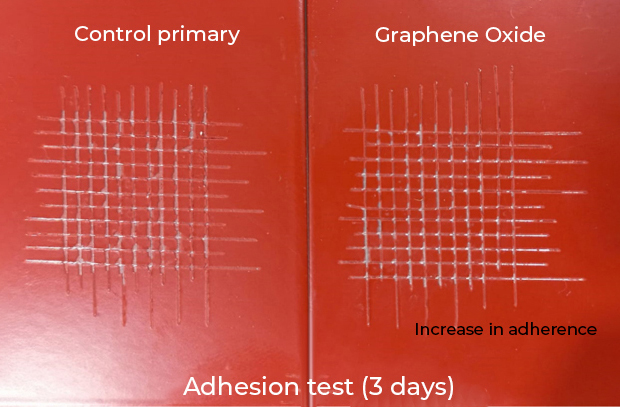
- More flexible coatings. The incorporation of graphene oxide not only improves adhesion, but also allows flexibility to the coating, allowing it to have high resistance to bending or greater resistance to fracture (Fig. 4).
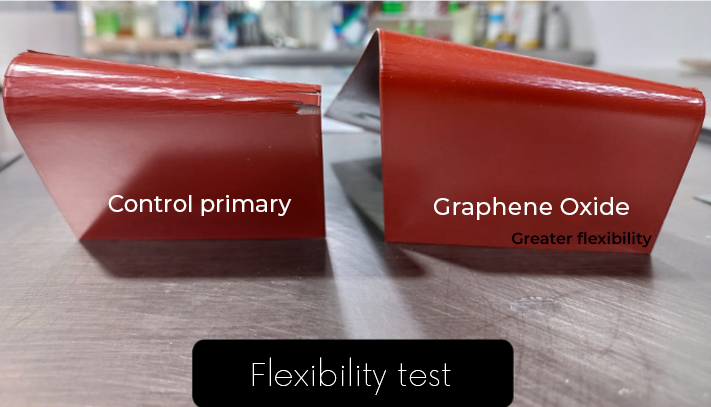
Referencias
- Chang, C.-H. et al. Novel Anticorrosion Coatings Prepared from Polyaniline/Graphene Composites. Carbon N. Y. 50, 5044–5051 (2012).
- Fengjuan Xiao, Chen Qian, et al., et al., Progress in Organic Coatings, 125, 79-88 (2018); doi.org/10.1016/j.porgcoat.2018.08.027
- Karolina Ollik and Marek Lieder. Review of the application of graphene-based coatings as anticorrosion layers. Coatings 2020, 10(9), 883. 2020.
- Zhang J., Kong, G., Li S., Le Y., Che C., Zhang S., Lai D., Liao X. Graphene-reinforced epoxy powder coating to achieve high performance wear and corrosion resistance. 20:1448-4160, 2020.
- Ghosh Tuhin and Karak Niranjan. Mechanically robust hydrophobic interpenetrating polymer network-based nanocomposites of hyperbranched polyurethane and polystyrene as an effective anticorrosive coating. New J. Chem., 2020, 44, 5980-5994.
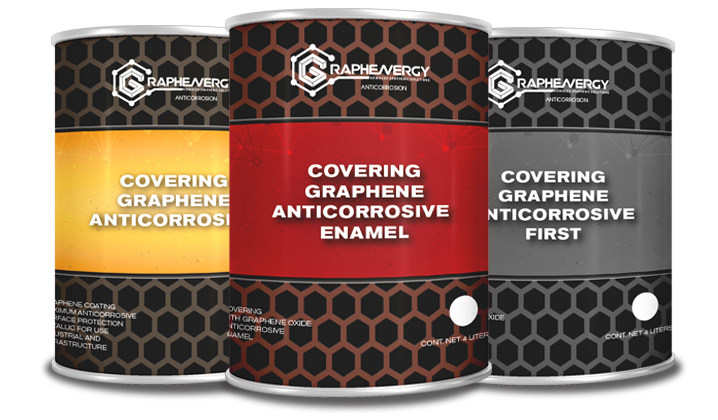