Innovation in the construction industry:
graphene oxide as an adjuvant to improve the resistance and durability of pavement
Concrete, due to its production efficiency, abundant sources of raw material, workability, and versatility, is a widely used material in the construction industry; among its numerous applications are rigid pavements for highways, airports, industrial floors and bridges, however, and despite its excellent resistance to compression, concrete presents limitations such as low tensile and flexural resistance that, together with factors such as overloads or environmental conditions, it usually develops failures such as cracking, perforations, detachment or erosion that will invariably require repair. Therefore, improving its quality, in addition to increasing its useful life and reducing risks, also allows maintenance work to be reduced or spaced out and, consequently, avoids the stoppage of operations or road closures, in turn representing significant economic savings.
In addition to quality and economy, another of the objectives of the construction industry is to reduce the carbon footprint, taking as a reference that the main concrete binder is cement and that, for each ton of cement manufactured, 1 ton of carbon is released. CO2 into the atmosphere. That is why there is a constant search for technologies and/or materials that improve or equalize the performance of concrete, in principle using a lower cement content through the use of cement substitutes such as mineral microparticles, an industrial waste product for example: fly ash, blast furnace slag or silica fume; reinforcements with steel, synthetic or glass fibers; resins and recycled materials such as tire rubber, polypropylene, PET or recycled concrete itself, as well as a wide variety of lignosulfonate, naphthalene sulfonate, melamine or polycarboxylate-based additives to provide plasticizing, water-reducing, setting accelerator or retardant functions, among other.
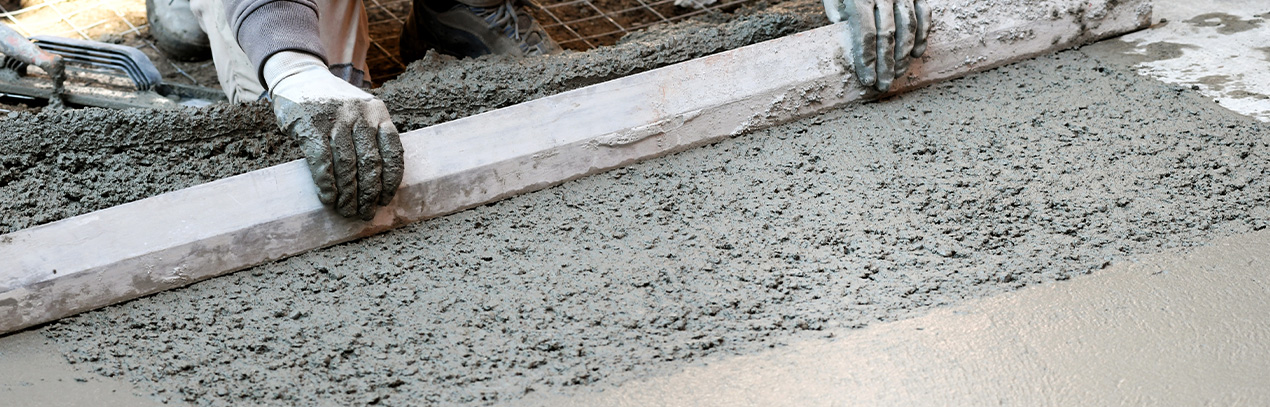
A valuable tool to add value in the triad: quality, economy and the environment, is nanotechnology, based on the premise that cement is mostly made up of C-S-H nanocrystals, responsible for the cohesive properties, hardening and, in definitively, of its mechanical resistance. This means that manipulating and modifying the structure of the cement from its nano level brings benefits at the macro level, that is, in the concrete as a finished product.
Throughout the last ten years of research and application of nanotechnology in construction, Graphene Oxide (GO) appeared on the scene, a carbon nanoparticle derived from graphite with excellent mechanical, thermal and barrier properties; Its good dispersion in water and great affinity for cement nanoparticles have shown interesting attributes to accelerate cement hydration, increase the production of C-S-H nanocrystals and reduce cement pores, which together represent important benefits in strength, durability and variety of infrastructure applications. Likewise, it has been shown that the manufacture of polymeric fibers for concrete modified with GO contributes to significantly improve its resistance to tension, impact, and abrasion, delays its deterioration due to corrosion or UV radiation and makes it more thermally stable, reduces cracking, among other benefits.
Derived from the great potential of this nanomaterial for the construction industry, in 2022 Sustainability magazine used the Web of Science (WoS) database to carry out an analysis of the research generated in the period 2010-2022 regarding the use of carbon dioxide. graphene in cement compounds. In this study, a total of 608 publications related to mechanical resistance, durability, thermal conductivity, among others, were identified, but only less than 10 journals made reference to the comprehensive benefits that GO offers to rigid pavements, either individually or as a three-dimensional reinforcement through the use of polymeric fibers, which represents a little explored application, but with large areas of opportunity.

Energeia – Graphenemex®, the leading Mexican company in Latin America in research and production of graphene materials for the development of applications at an industrial level, through its Graphenergy Construction® product line in 2018, placed an additive on the market for the first time for concrete with graphene oxide that contributes to improve the microstructure of cement-based conglomerates from their initial stages. Subsequently, in 2020 and thanks to its extensive experience in handling nanocomposites, it developed a new generation of polymeric macrofibers with graphene nanofilling. The benefits that GO offers at the nano and micrometric level have been evaluated in the laboratory and in the field on concrete macro designs, obtaining excellent results in terms of workability, density, impermeability, heat dissipation, setting, appearance and with balanced mechanical contributions of resistance to compression, tension, flexibility and abrasion that together complement the economic, environmental and quality needs of rigid pavements, among many other cement-based structures. Its use is very simple and does not require additional equipment or processes to those regularly used in construction, in addition to allowing adjustments in its handling, dosage and use in conjunction with other additives to improve its performance.
Drafting: EF/DHS
References
- Houxuan Li, et al., Recent progress of cement-based materials modified by graphene and its derivatives. Materials 2023, 16, 3783. 2. I. Fonseka, et al., Producing sustainable rigid pavements with the addition of graphene oxide. 2023; 3. Byoung Hooi Cho., Concrete composites reinforced with graphene oxide nanoflake (GONF) and steel fiber for application in rigid pavement. Case Stud. Constr. Mater. 2022; 17: e01346; 4. Kiran K. Khot, Experimental study on rigid pavement by using nano concrete. Int Res J Eng Techno, 2021; 08: 07,4865; 5. Jayasooriya, D. et al., Application of graphene-based nanomaterials as a reinforcement to concrete pavements. Sustainability 2022, 14, 11282; 6. Sen Du, et al., Effect of admixing graphene oxide on abrasión resistance of ordinary portland cement concrete. AIP Advances. 2019; 9: 105110; 7. D. Mohottia, et al., Abrasion and Strength of high percentage Graphene Oxide (GO) Incorporated Concrete. J. Struct. Eng. 2022; 21: 1; 8. Fayyad, T., Abdalqader, A., & Sonebi, M. An insight into graphene as an additive for the use in concrete. In Civil Engineering Research Association of Ireland Conference 2022 (CERAI 2022): Proceedings (CERAI Proceedings).