Glass and Carbon Fiber Composites Enhancement:
Improving Properties with Graphene Nanoparticles
Glass and carbon fibers, thanks to their excellent properties, are widely used in industries such as aerospace, maritime, automotive, sports, construction, and even in the manufacturing of fundamental components for renewable energies such as wind power. However, despite their excellent performance, they often exhibit a phenomenon known as “interlaminar delamination” due to weak fiber/resin interfacial interaction, which can compromise the product’s lifespan and safety due to their significant role in stress transfer between both elements. As this interaction is key to the long-term success of composite structures, various improvement alternatives have been explored, such as Z-pinning, stitching, and braiding; increasing the surface area and reactivity of fibers through surface modifications such as plasma treatment, thermal modification, or chemical functionalization, which are complex, costly processes that are not always efficient and tend to reduce the laminate’s in-plane performance.
“As an additional strategy of relatively recent emergence, the incorporation of nanoparticles into fiber composite materials was proposed to favor interaction with the embedding matrix.”
Graphene, the nanomaterial known as the cornerstone of the carbon family and which since its isolation has been described as “the material of the future” or “the miracle material,” is an attractive candidate as a nanoreinforcement for countless polymeric compounds due to its unique graphitized flat structure, which leads to better mechanical, thermal, and other properties that, unlike other nanoparticles such as carbon nanotubes (CNTs), do not significantly increase resin viscosity and therefore allow higher concentrations to be incorporated, favoring the aforementioned fiber/matrix interaction.
Research on the effects of graphene for the design of hybrid materials based on fibers (glass/carbon) embedded in a commonly epoxy-based polymeric matrix has highlighted greater compound stiffness, improvements in fracture resistance, better lubrication, and even improved electrical conductivity. This is because its large surface area allows effective load transmission from the soft polymer matrix to the relatively stiffer graphene sheets, which is an essential requirement for improving mechanical performance, confirmed by increased interlaminar shear strength of the material, greater tensile and impact strength. Additionally, during the manipulation and cutting of hybrid fiber structures, the presence of graphene contributes to generating less heat during milling, leading to lower cutting temperatures and smoother surface roughness; likewise, another benefit is that graphene produces a greater hardening effect and better bending resistance of the material exposed to different temperatures ranging from 40 °C to 200 °C.
At Energeia-Graphenemex, the leading company in Latin America in the production of graphene materials and in the development of applications, we are convinced that graphene’s extraordinary capabilities as a nanoreinforcement for countless three-dimensional matrices will continue to encourage researchers and industrial colleagues to explore its benefits for the manufacture of stronger and lighter structural components for aircraft such as fuselage and wings; automotive parts and aerodynamic bodywork; wind turbines, sports equipment, construction materials, among others.
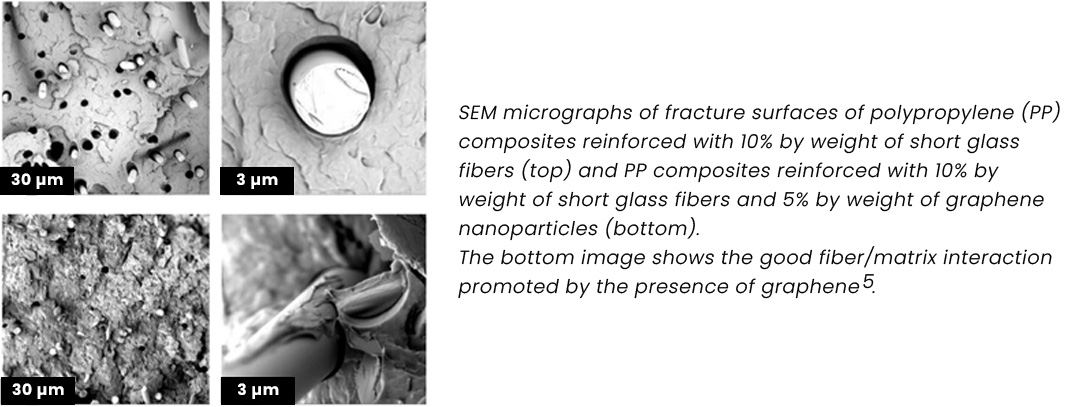
Draft: EF/DH
References:
- Effect of dispersion of alumina nanoparticles and graphene nanoplatelets on microstructural and mechanical characteristics of hybrid carbon/glass fibers reinforced polymer composite. Journal of material research and technology. 2021, 14, 2624;
- Experimental investigation on the properties of glass fiber-reinforced polymer composites containing Graphene. AIP Conf. Proc. 2022, 2405, 050009;
- Reinforcement effect of graphene oxide in glass fibre/epoxy composites at in-situ elevated temperature environments: An emphasis on graphene oxide content. Composites part A: Applied science and manufacturing. 2017, 95, 40;
- Preparation and Mechanical Properties of Graphene/Carbon Fiber-Reinforced Hierarchical Polymer Composites. J. compos sci. 2019, 3, 30;
- Improving fiber/matrix interfacial strength through graphene and graphene-oxide nano platelets. IOP Conf. Ser.: Mater. Sci. Eng. 2016, 139, 012004;
- Effect of Graphene on Machinability of Glass Fiber Reinforced Polymer (GFRP). J. Manuf. Mater. Process. 2019, 3, 78;
- Size effect of graphene nanoplatelets on the morphology and mechanical behavior of glass fiber/epoxy composites. J Mater Sci. 2016, 51, 3337.